It’s a small building, inconspicuous in the clutter of assembly halls, machine shops, engine plants, etc., which go to make up the Triumph factory complex in Coventry. Yet, over 200 cars per week pass through it, all being tested in the most exacting manner for different world markets. Most of these are cars destined for the United States and 100% of cars for California are tested.Just what is this small but important facility? It’s the Quality Exhaust Emission Test Laboratory, established to deal with all aspects of Triumph production exhaust emissions, not only from the point of view of North American and European government standards but from a simple quality control view as well. Approximately ten vehicles are on test at any given moment, supervised by a staff of twenty, including engineers, technicians and clerical staff. There are two basic test areas.
1. Steady State Idle Test Area:
Here, cars are first checked for proper operation of emission control components and for correct timing and carburetion. Reading of hydrocarbon and carbon mon-oxide emissions are taken on Olsen Horiba exhaust analyzers and testing is done on Sun Engine Tune equipment.
2. Single Cycle Testing:
This is done on Redman Heenan Rolling Roads, a type of chassis dynamometer which produces the actual con-ditions of road travel while the car never moves out of the test bay. Exhaust analysis is carried out while the test car moves over the imaginary road and each car’s perfor-mance is automatically read out by a computer.
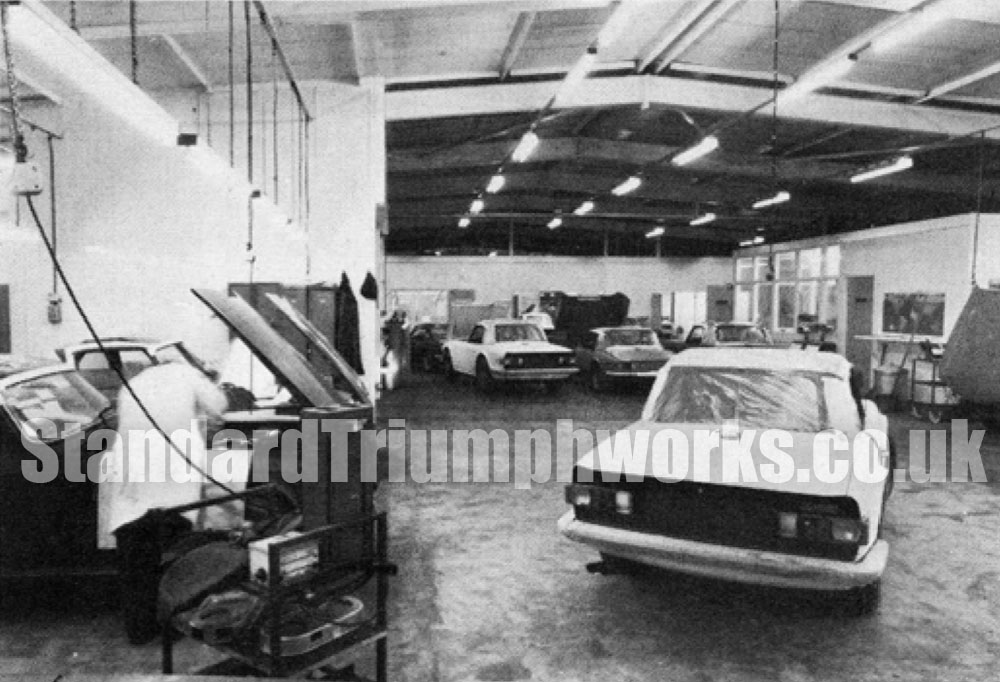
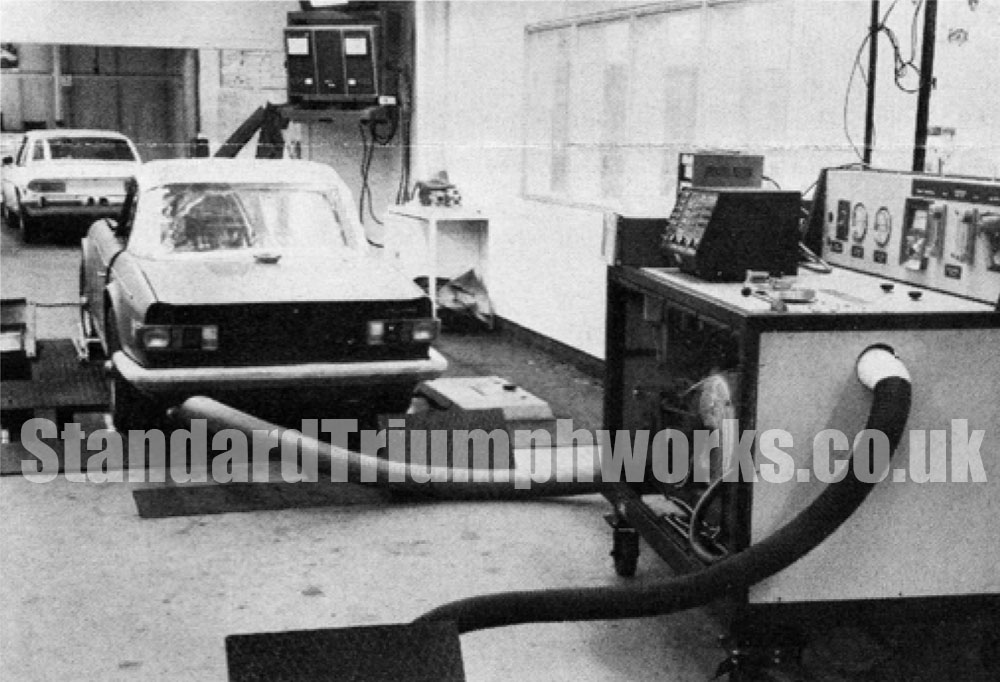
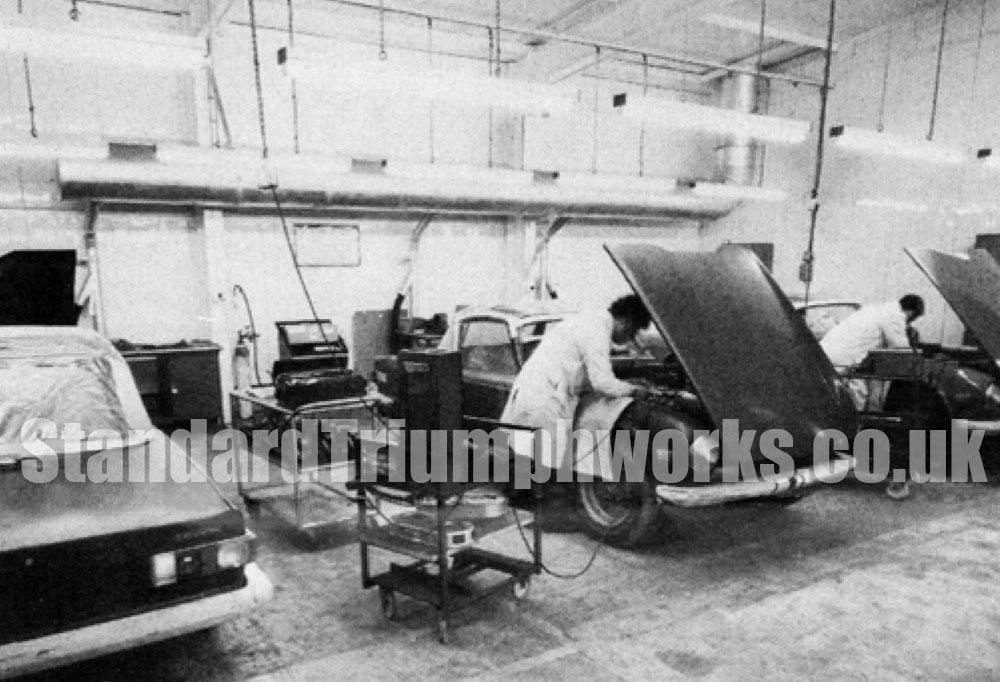
The continual testing of normal production cars for emission control capability is now an integral part of every manufacturer’s new-car test procedure. It does not replace the normal tests for proper component functions which are carried out at the end of the assembly line. Instead, it adds another step before the car can be shipped out to its destination, making certain that the product is right before it gets to the customer.